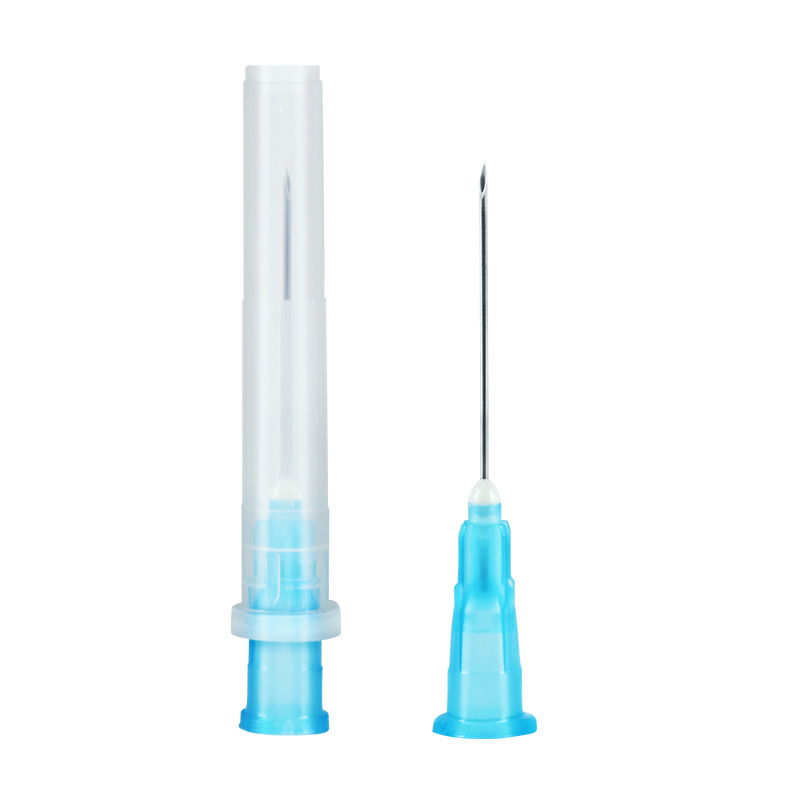
机器视觉检测注射针头是一种利用计算机视觉技术对注射针头的各种特性进行检测的高效方法。
一、检测内容
-
外观缺陷检测
- 划痕检测:注射针头表面的划痕可能会影响其使用性能。机器视觉系统通过高分辨率的相机拍摄针头表面图像,然后利用图像处理算法分析图像。例如,通过边缘检测算法来突出划痕的边缘部分。如果划痕的长度、深度(通过灰度变化等方式间接判断)超过设定的阈值,系统就会判定该针头为不合格品。
- 毛刺检测:在针头的制造过程中,可能会产生毛刺。机器视觉可以从不同角度拍摄针头图像,然后对其轮廓进行分析。通过比较实际轮廓与标准轮廓模型,识别出超出正常范围的突出部分,即毛刺。例如,采用基于轮廓拟合的方法,将针头的实际轮廓与理想的光滑轮廓进行对比,当拟合误差超过允许值时,判定存在毛刺。
- 弯曲检测:弯曲的注射针头是不符合质量要求的。机器视觉系统可以从多个视角获取针头的形状信息,利用三维重建技术(如果需要高精度检测)或者基于二维图像的形状分析方法。比如,通过霍夫变换等直线检测算法来检测针头主体部分是否为直线,计算直线的弯曲程度来判断针头是否弯曲。
-
尺寸精度检测
- 针头长度检测:准确测量注射针头的长度是很重要的。机器视觉系统可以通过在图像中建立合适的坐标系,根据像素与实际尺寸的比例关系来测量针头长度。例如,在相机经过标定后,知道每个像素对应的实际长度单位,通过计算针头在图像中的像素长度,从而得到实际长度。如果测量长度与标准长度的误差超过一定范围,则判定为不合格。
- 针头直径检测:对于针头的粗细检测也很关键。利用机器视觉的边缘检测算法找到针头的外边缘,通过测量边缘之间的距离来确定直径。可以采用最小二乘法拟合圆等方法来精确测量直径。同样,将测量值与标准直径对比,判断是否合格。
-
针孔质量检测
- 针孔通畅性检测:机器视觉可以结合其他技术,如气压检测。首先通过机器视觉定位针孔位置,然后在针头一端施加一定压力的气体,在另一端利用传感器(可以是光学传感器等)检测气体是否顺利通过。同时,机器视觉可以观察针孔周围是否有堵塞物的迹象,如通过观察针孔周围的透明度变化等情况来辅助判断针孔是否通畅。
- 针孔形状检测:通过拍摄针孔的高分辨率图像,利用图像处理技术分析针孔的形状。例如,采用形态学处理方法来确定针孔是否为规则的圆形,通过计算圆形度等形状参数,与标准的针孔形状参数进行比较,判断针孔形状是否合格。
二、检测系统组成
- 照明系统
- 照明系统对于获取高质量的注射针头图像至关重要。由于注射针头通常是金属材质,表面反光较强,需要合适的照明方式来减少反光。可以采用环形光源,它能够提供均匀的光照,减少阴影,使得针头表面的细节能够清晰地被相机捕捉。例如,在检测针头表面划痕时,环形光源能够照亮整个针头圆周,避免因光照不均而导致的划痕误判。
- 图像采集系统
- 包括工业相机和镜头。工业相机需要根据检测精度的要求选择合适的分辨率。例如,对于高精度的针头表面缺陷检测,可能需要使用百万像素甚至更高分辨率的相机。镜头的焦距和视场角也需要根据针头的大小和检测范围进行调整。例如,短焦距镜头可以获得较大的视场角,适合对整个注射器具(包括针头和针筒)进行整体拍摄;而长焦距镜头可以用于对针头细节进行放大拍摄。
- 图像处理与分析系统
- 这是机器视觉检测的核心部分。它运行各种图像处理算法和机器学习模型(如果采用基于学习的方法)。图像处理算法包括滤波算法(如中值滤波去除噪声)、边缘检测算法(如 Canny 边缘检测)、形态学算法(如腐蚀和膨胀用于处理形状特征)等。机器学习模型可以是基于深度学习的卷积神经网络(CNN),经过大量标注的针头图像数据进行训练,用于自动识别针头的各种缺陷类型。例如,通过训练好的 CNN 模型,能够直接对输入的针头图像进行分类,判断是合格产品还是有划痕、毛刺等缺陷的不合格产品。
- 控制系统和执行机构
- 控制系统用于协调照明系统、图像采集系统和图像处理系统的工作流程。例如,控制相机的拍摄时间、照明的强度等。执行机构则根据检测结果采取相应的行动。如果检测到不合格的注射针头,执行机构可以将其从生产线上分拣出来,通常采用机械臂或者气动装置等将不合格品移动到指定的回收区域。
三、优势
- 高精度和稳定性
- 机器视觉检测能够提供高精度的检测结果,不受人为因素(如疲劳、情绪等)的影响。它可以持续稳定地工作,保证检测质量的一致性。例如,在尺寸检测方面,机器视觉系统的精度可以达到微米级别,远远高于人工检测的精度。
- 高效率
- 能够实现高速检测,适应现代化生产线的快节奏。例如,一个先进的机器视觉注射针头检测系统可以在每秒检测数十个甚至上百个针头,大大提高了生产效率。
- 数据记录和追溯
- 可以记录每个注射针头的检测数据,包括图像数据、检测结果等。这些数据可以用于质量追溯和统计分析。例如,当发现一批产品出现质量问题时,可以通过查阅检测记录,快速定位问题的根源,如特定生产批次的原材料问题或者生产设备故障等。